Pioneering with Robot Bike Co.
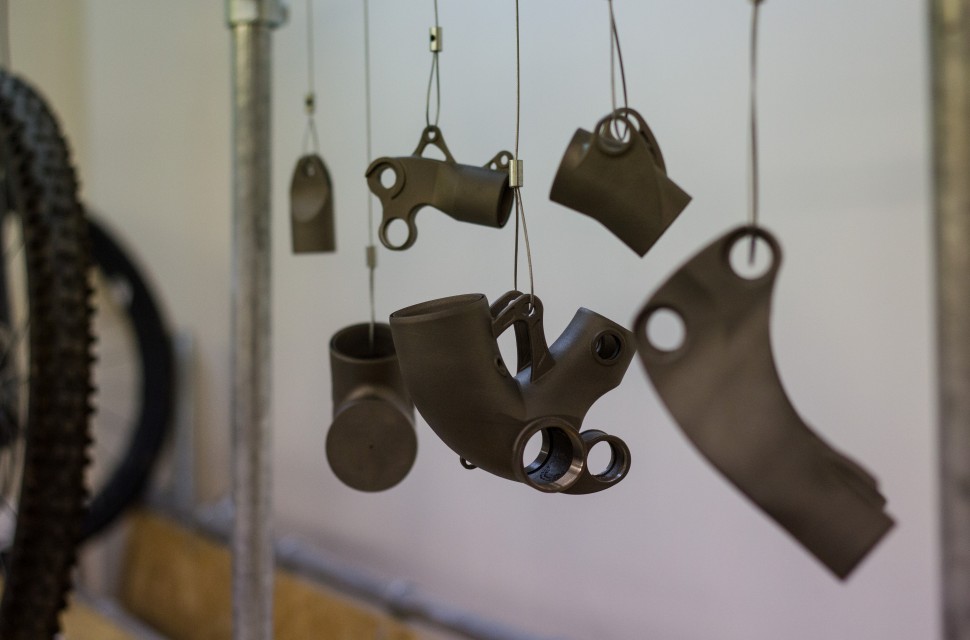
An invite into the Robot Bike Co. workshop was an opportunity too good to miss, a chance to delve deep into the mind boggling world of additive manufacturing and bike design. A time to bend our brains around the concept that is the custom creation of titanium lugs and carbon tubing making up the foundations of this innovative company and, of course, take an R130 for a ride!
Founded back in 2013, Robot Bike Co. is the coming together of some great minds, each with different experiences and skills that when collected together alongside the pure love for bikes, create a force to be reckoned with. From an additive manufacturing expert to an aerospace engineer and material scientist, a CAD expert, a frame builder and ex journo, finally to those with business heads to make sure the whole party ends as it should, Robot Bike Co. is one awe inspiring place to be.
Stepping in though the door of Robot Bike Co. HQ in the sleepy hills on the outskirts of Monmouth, Wales, the workshop is as clinical as you’d expect it to be from a company utilising the clean and precise connotations that the word ‘robot’ conjures up. On hand to talk to us are Ed, Andy, Rob and of course a trail dog. We haven’t been to a bike manufacturer yet without one of these furry beasts, causing us to conclude it must be an important part of the recipe.
Robot Bike Co. are at present, producing two bikes, the R160 a 27.5” 160mm enduro rig and the R130, a 130mm 29er, but the length of travel is the only thing that can or will be similar between any two bikes. Customers can completely customise the geometry of bike from angles, to tubing lengths and sizing. Most angles and lengths can be configured to your liking, making bike you create completely bespoke, it’s not just a choice of longer or shorter, big or small within the range.
We were, of course, eager to learn just how these mechanical and raw looking beasts are formed, so without even a coffee in hand we launched into the technical aspects of the bike and a lesson in science from Ed. First up, those lugs are formed through additive manufacturing, 3D printing to use its layman’s term but don’t tell Andy we said that! the process is crazy to think about and even crazier to watch (see videos below).
The titanium additive manufactured lugs are first created by a computer programme defining the exact shape of the lug given the geometry that has been decided. Then high power lasers, yes lasers, basically melt layer upon layer of titanium powder into shape, the melting process creating essentially one piece of material. The laser gets to work, then after the power is melted, the laser pauses and a new layer of powder coats the work surface and the laser then continues work, so on and so forth until a lug is born. Ed says the use of titanium isn’t just an excuse to use a fashionable material, it produces the optimum weight to strength ratio for the loaded areas of the frame.
Ed also threw a lot more technical talk about ‘topology optimisation’ at us, this is how the material layout of the lugs is optimised for it’s given load. For example, the thickness of the lug wall is finely controlled so to ensure the frame is as strong as it needs to be without adding unnecessary weighty material where it's not needed. It’s something that’s easy to carry out in conjunction with additive manufacturing and results in the bikes being offered with a lifetime frame guarantee.
The lugs are manufactured in the UK at Renishaw and sent, perfectly formed and bubble wrapped to the Robot Bike Co. workshop ready for Ed to create a bike. Of course, the lugs are only one part of the build process, the carbon tubing is the other part. Robot Bike Co. use unidirectional carbon fibre tubes and uniform tube shapes, there is no ‘criss-crossing’ of the fabric as you might find in woven carbon fibre or alternative shaped tubes here, meaning the frame will be stronger and stiffer due to the fibres of the material being kept in close alignment with the loading direction when being ridden. Where much of the manufacture of a Robot bike is kept within the UK, the carbon tubes couldn’t come from further away. New Zealand in fact, from a company making top class sailing masts. Ed told us that the reason so this is that he simply can’t get the same quality of tubes in the quantities he wants cheaper anywhere else.
On receiving the box of parts, including head tube, seat tube and bottom bracket junctions, chain stay yoke and drop outs work begins on the build. Ed will have already cut to length the carbon tubing required for the customer specifications of the bike and so now all that remains is for the pieces to be glued in place.
Our engineering lesson continued as we learnt about ‘double lap shear joints’, the process of bonding the carbon tubes to the lugs. Each and every junction features two layers of titanium material into which the carbon tube slots. This area is filled with aerospace-grade two-part epoxy Henkel adhesive, and the carbon tube is inserted. Ed says this process ensures that there is an even coverage of adhesive. Merely trying to adhere two surfaces together would risk some parts being covered by only a thin layer of glue, thus reducing the strength, the use of double lap shear joints negate this worry. After all, if its good enough for planes, it’s good for a bike, right? Robot Bike Co. say “Aerospace surface preparation practices combined with our design and Additive Manufacturing process means that Robot Bike Co.’s joints are more efficient than any others known to be use in aerospace or Formula 1 applications. For you, this means the lightest weight and most reliable frame possible.” Ed told us he’s tested a drop out and ‘hung’ the equivalent of a 4x4 Jeep off the end of the glued in carbon tube and still the adhesive didn’t fail, the 10mm allen key used to through the drop out to secure it sheared first!
Using specific jigs, aligned for the customers chosen sizing, Ed assembles the frame and if the customer requires a full bike build, he builds it up with all the parts too. The only part we haven’t mentioned here is the rocker link, this is made from aluminium just next door where the guys in the adjacent workshop are not only bike nuts too, they make parts for Formula 1 cars.
Whilst we on the topic of surprising industry in Monmouthshire whilst watching Ed clean up the workshop with a huge roll of thin white material he hit us with astonishing fact number two – the Forest of Dean is home to a huge paper mill manufacturing tea bag (yep, like a good old brew) material globally. Ed gets a spare roll every now and again as an absorbent workshop clean-up aid!
After all that science, we left Robot Bike Co. with an R130 to review and get to grips with the in and out’s of the bike, the suspension and crucially how it rides. A visit to Robot Bike Co. has broadened our horizons of bike building and widened our concepts of what is possible. It has shown us that there is technology used in other industries that can be completely applicable to bike, it just needs the right minds and passion to bring the ideas to fruition.
The guys behind Robot Bike Co. are just such people, the dream they had to build custom bikes, unique and specific to the application is a reality. They are bringing new technology to an ever developing industry, one that is proving to have great success too with custom from innovators such as themselves from all over the world. A bike from Robot Bike Co. will never be just a bike, you are buying part of a pioneering concept, you will be part of the drive, showing the world what is and what can be possible and that is exciting, very exciting.
You might also like:
- Feature - Keeping it real: The BTR Fabrications Story
- First Ride: BTR Fabrications Pinner
- First Ride: Bird Cycleworks Aeris 145